The evolvement of Digital Two-Way Radio has introduced significant complexities in the design, implementation and ongoing maintenance, support and operations of new digital radio systems. Concurrently, Public Safety and Mission Critical organizations are now conducting very thorough due diligence in the technical specifications, functionality, performance criteria, application development, standards compatibility and systems testing when making a technology decision. Is this same level of due diligence being expended in the selection of your Systems Integrator?
Digital Two-Way Radio systems today are much different than legacy analogue systems of the past. They are software driven. They have operating platforms. They support an ecosystem of 3rd party applications. The life expectancy of a digital radio is closer to 7 years than the previous industry standard of up to 15 years on analogue. Firmware upgrades are common, particularly with embedded applications, and these can occur annually. A missed firmware upgrade can have a direct impact on the performance of not only the radio system, but the applications that it supports and the devices it interoperates with. If this is not managed strategically and methodically, safety of the radio user can be jeopardized.
Is your integrator an authorized channel partner of the manufacturer you have selected, and specifically, are they authorized to service, maintain or deploy the specific system you have selected? Consider the following in your due diligence of a systems integrator:
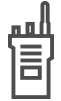
1: Authorization Matters – A non-authorized integrator may not have the required manufacturer training to support the programming and configuration of products or systems that you have selected, and they may not have the required programming software, or the capability to install, troubleshoot or repair the products you have selected. Further, a non-authorized integrator may not have direct access to your selected Manufacturers’ Technical support, future firmware or software releases, or general product information bulletins.
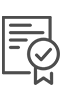
2: Qualifications of Personnel – Most often the system design requires sign-off by a Manufacturer certified integrator. Ask your potential integrator to produce evidence of their certification training specific to the system you have selected. Ask the Manufacturer to verify this.
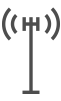
3: Testing – There are very specific test procedures that must be followed in order for your system to operate as expected. Ensure your integrator is fully factory trained and has the required test equipment. Ask for evidence of their test equipment calibration policies. Does it match the Manufacturers’?
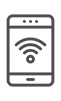
4: Guarantee – Products that are not provided, installed or commissioned directly by a Manufacturer authorized integrator may be void of any warranty, and your Manufacturer may not guarantee the performance of their products that are procured through non-authorized channels.

5: Drawings – Are as-built drawings required? Does your integrator have the capacity to produce these, and have you seen samples of their work?
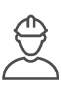
6: References – Does your Integrator have references from other Mission Critical customers for deployments of the same technology you have selected. Do they have references from the Manufacturer you have selected?
Your Technology investment can be in the many tens of thousands, if not hundreds of thousands of dollars. Make sure your due diligence on your LMR systems integrator is consistently as thorough as the technology, or you may end up with a system that does not perform to your expectation.
Leave A Comment
You must be logged in to post a comment.